Rotary Micro Stages
M3-RS Rotary Smart Stage
Angular Micro positioning module with embedded controller
Smallest size, high resolution, unmatched ease of use
This miniature, “all-in-one” rotary positioning stage has closed-loop position resolution better than 0.022 degrees with absolute position feedback. it provides point-to-point angular positioning with closed-loop bandwidth of ~100Hz.
All drive electronics, embedded firmware, patented piezoelectric motors, position sensors and bearings are integrated into a module less than 12 x 22 x 16 mm. With no need for an external controller, this smart stage enables smallest system size in hand-held and portable instruments.
The embedded controller also means rapid and easy integration into your system. It accepts direct input of high-level digital motion commands from your system processor over UART, SPI, I2C or analog servo interface. It needs only 3.3 V DC and can be powered by USB or standard batteries.
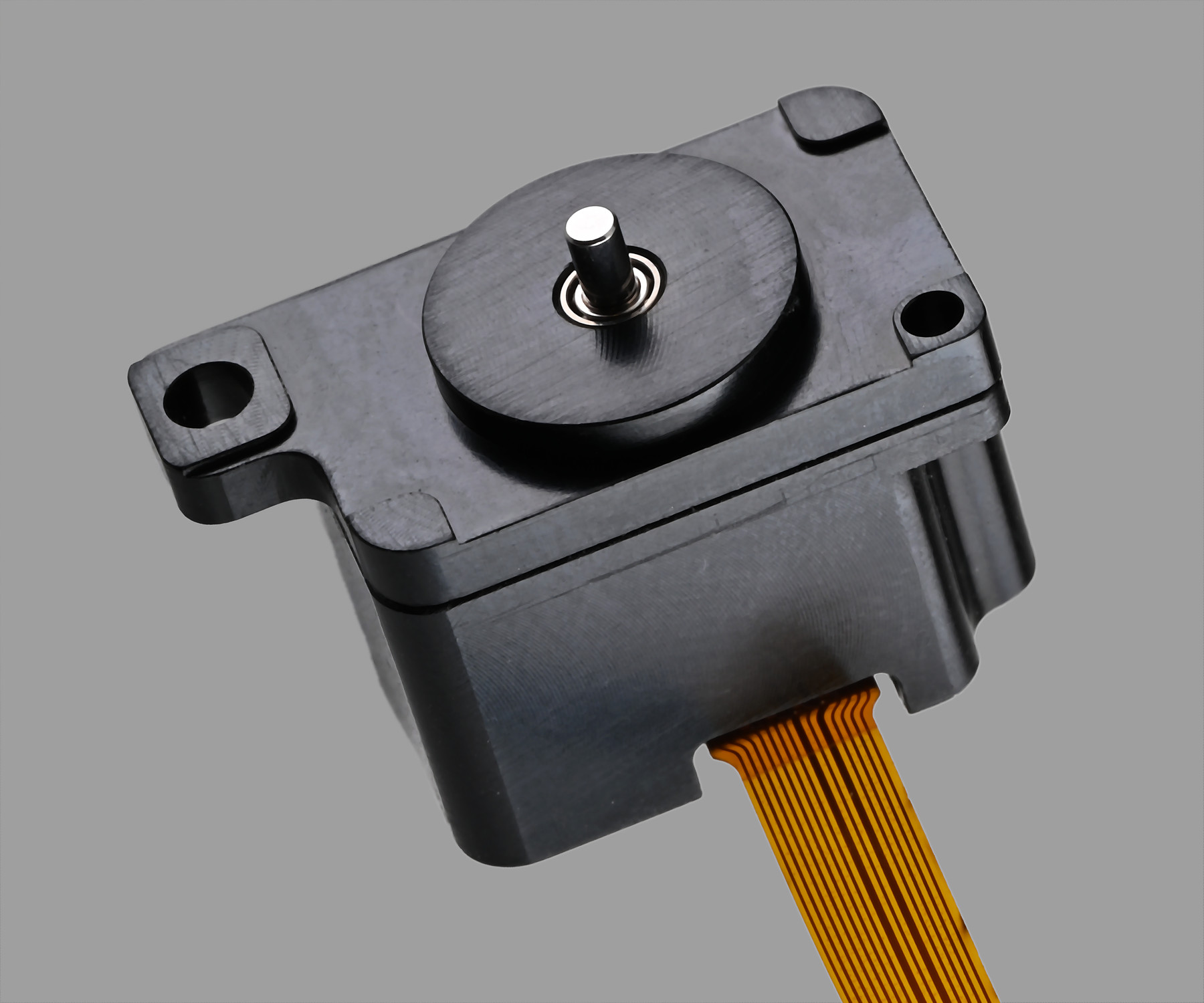
M3-RS-U2 Rotary Stage – This piezoelectric stage provides continuous 360° rotation with absolute position feedback. Contact us for guidance on mounting a payload to the rotating shaft for your OEM application.
Advantages
- Smallest size: 11.75 x 21.9 x 16 mm including controller
- Closed-loop controller embedded in micro stage
- No separate electronics needed
- 3.3 VDC input
- Direct input of motion commands (I2C, SPI, UART or analog servo)
- Angular resolution ~ 0.022 deg closed loop
- Absolute encoding and position feedback
- Millisecond step and settle times
- Point-to-point angular positioning with closed-loop bandwidth ~100Hz
- Holds position with zero power and no jitter
- Fast integration for embedded motion in smaller instruments
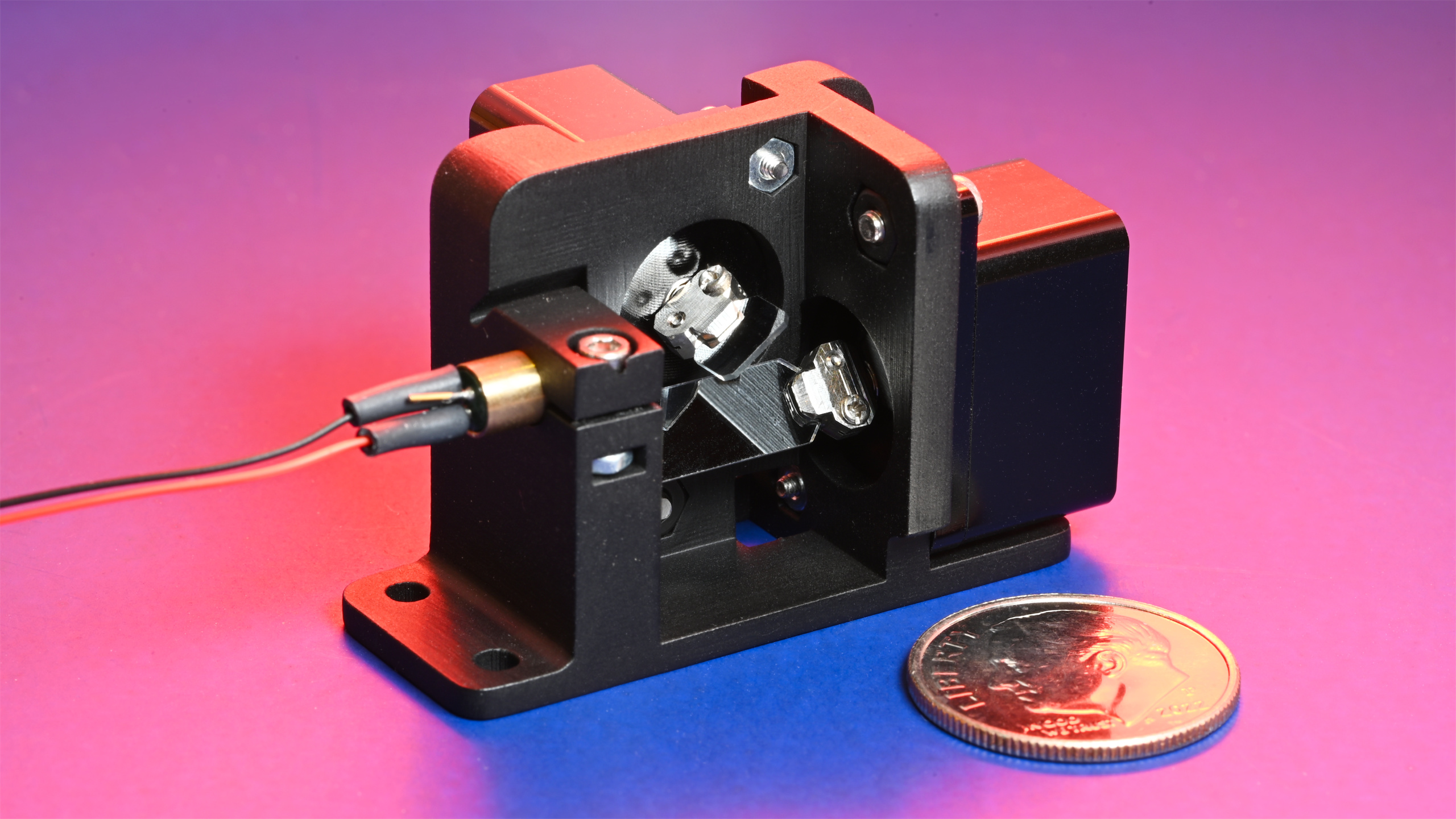
M3-RS-U2 Rotary Stage shown with mirror (not included) mounted on rotating shaft for point-to-point beam steering. Contact us for guidance on payload mounting and/or custom clamps for OEM applications.
Applications
Scientific and industrial instruments requiring precise rotational positioning in a limited space, including:
Medical
- Next-gen sequencing (NGS)
- Dermatology lasers
- Fluorescence microscopes
- 3D imaging instruments
- In-vivo and in-vitro micro laser surgery
Telecommunications
- Free-space optical communication
- Variable optical attenuation
- Fiber-to-fiber optical switching
Industrial
- Quantum Computing
- 3D printers
- LIDAR, 3D measurement, spectroscopy
- Remote sensing (e.g. pollution)
- Laser marking and machining
Aerospace and Defense
- Target designation, jitter compensation
- Automated obstacle detection, tracking and avoidance for robots, UAVs, etc.
Application Example and Developer’s Kit: Two-axis, two-mirror beam steering system.
Developer’s Kits
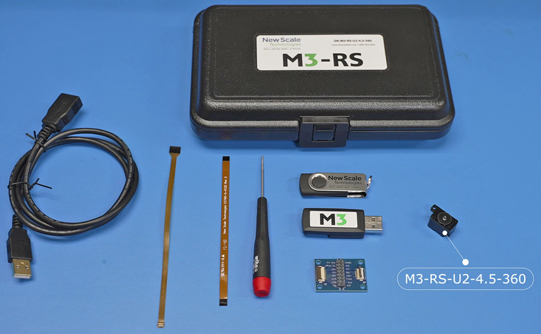
DK-M3-RS-U2-4.5-360
Developer’s Kit: Rotary Microstage
- One M3-RS-U2-4.5-360 Rotary Smart Stage with embedded controller
- Straight FPC
- Breakout board for evaluation and development
- USB adapter and extension cable
- New Scale Pathway™ Software
- Screwdriver and mounting screws
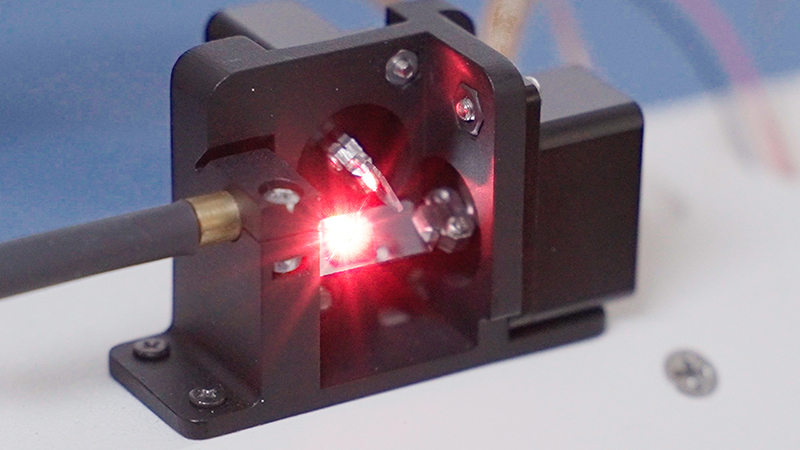
DK-M3-RS-U2-2M-20-L
Developer’s Kit: Two-Axis Two-Mirror Beam Steering System
- Two M3-RS-U2-4.5-360 Rotary Smart Stages with embedded controller and straight FPC
- One M3-RS-U-Mirror-01-03, mounted to stage
- One M3-RS-U-Mirror-01-11, mounted to stage
- One 650nm collimated laser
- Base
- Demo board and cables for evaluation and PC connection
- Power supply
- New Scale Pathway™ Software
Specifications
M3-RS-U2-4.5-360 Rotary Smart Stage | Download Data Sheet (PDF)
Attribute | Value |
---|---|
Range of motion | 360 degree continuous rotation |
Speed | >1100 deg/sec |
Acceleration* | >1,000,000 deg/sec² |
Stall torque (min) | 0.04 N-mm |
Holding torque (min) | 0.08 N-mm (zero power) |
Recommended maximum payload mounted to rotating shaft (payload must be balanced) | |
Mass | 3 g |
Inertia | 350 g-mm² |
CLOSED-LOOP performance (with built-in position sensor) | |
Recommended step frequency | up to 100 Hz |
Resolution (absolute encoder resolution) | 0.022 deg absolute |
Repeatability | +/- 0.05 deg (880 µrad) |
Accuracy | 0.25 deg (4400 µrad) |
Closed loop step & settle times (typical)* | 0.5 deg step: 16 ms 5 deg step: 22 ms 20 deg step: 31 ms |
OPEN-LOOP performance (external position sensor provided by user – see application note) |
|
Open loop step & settle times (typical)* | 0.05 deg step: 0.5 ms 0.5 deg step: 1.2 ms 5 deg step: 5 ms 20 deg step: 11.2 ms |
Input voltage | 3.3 VDC +/-6% |
Power consumption (typical) | 750 mW active, moving 190 mW active, ready 150 mW standby |
Stage mass | 4.7 g |
Operational lifetime | >2 million random positions or seven years, whichever occurs first |
Temperature and relative humidity | 0 to +60 °C, non-condensing |
Conformance | RoHS; CE pending |
Controller | Integrated into stage, 64 MIPS no external controller needed |
Communication interface: | I²C, SPI, or UART Input directly to M3-RS |
*With 0.6 g-mm2 inertial load mounted to output shaft, based on a target tolerance of 2 encoder counts
documentation
Download CAD files, New Scale Pathway software and programming guides (registration required)
Learn More
The M3 Smart Module Platform
M3 Smart Modules integrate a piezoelectric SQUIGGLE® micro motor, precision mechanical guide system, position sensor, microprocessor, and drive electronics into one tiny package. Eliminating the need for external controllers, they offer the smallest system size and easiest integration into OEM systems.
Custom Engineering
We use our configurable M3 Smart Module platform to develop custom motion modules and systems that meet your exact requirements. We also develop full-custom micro motion systems. Ask us about a motion system feasibility study, the first step to faster, lower-risk product development.